The challenge
Intelligent completion systems are the best option for selecting production zones, ensuring efficient reservoir management, and increasing oil recovery of oil and gas fields. However, hydraulic systems’ low reliability and multiplex limitations still hamper their full use.
Our solution
The eICV is a highly reliable inflow control valve based on a fully electric actuation system integrated with a well monitoring system. This innovative equipment allows precise injection or production flow control in deepwater wells over extreme temperatures, high pressures, and significant flow rates.
The eICV is a highly reliable inflow control valve based on a fully electric actuation system integrated with a well monitoring system.
The infinitely variable choke and sophisticated flow production profile allow optimal production and injection control of each zone in the reservoir. In addition, multiple eICVs can be installed in the well, sharing a single downhole cable with the wholly integrated well monitoring system, thus increasing oil recovery and reducing operational costs.
The all-electric completion system is the best choice for well-production management. It has a robust concept, a compact design, and advanced control and feedback sensing systems.
Main Advantages
- Electrically operated
- Multiple valves sharing a single electrical cable in the same well
- Infinitely variable choke
- Fast, bidirectional changes in the choke position
- Redundant sensing systems for choke position, feedback, and diagnostics
- Integrated pressure and temperature sensors to monitor annulus and tubing spaces
- Erosion-resistant trim with tungsten carbide inserts
- High axial driving force to remove scale build-up on the choke trims
- Open/close mechanical override system using standard wireline methods
- Long life cycle with high reliability in harsh environments
- Designed for extreme temperatures, high pressures, and significant flow rates
- Many valves can be installed in the well, sharing a single electric cable
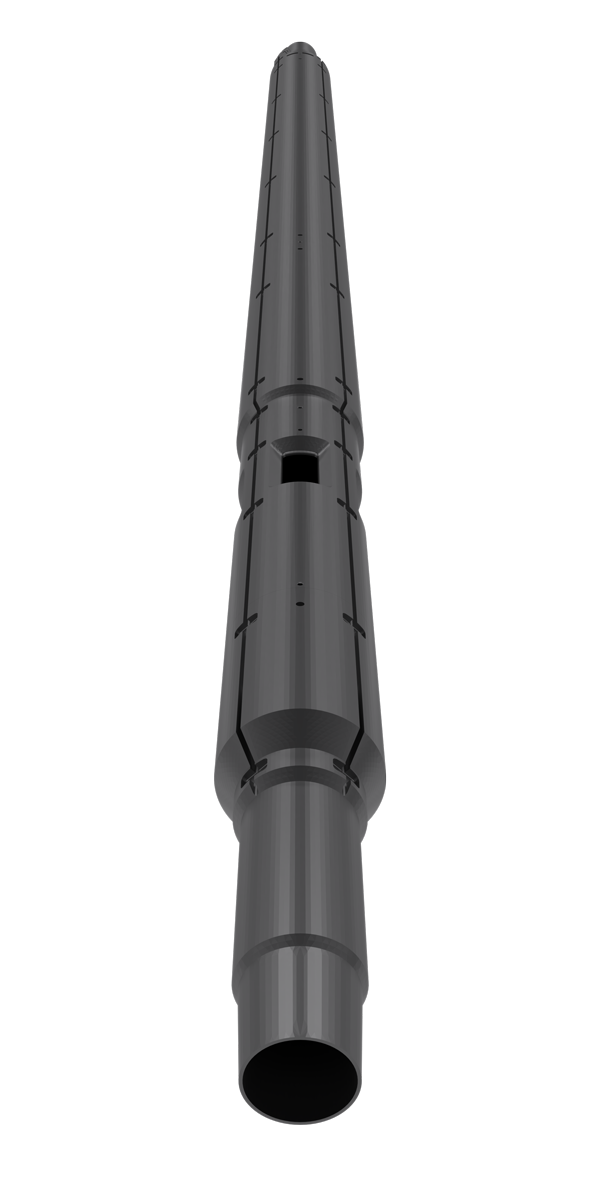
Get inContact
Fill in your contact information
and we’ll get back to you shortly.
Papers
Abstract
Brazilian Pre-Salt wells located in ultradeep water, capable of producing 70,000 barrels per day, have been, for years, strong candidates for Electric Intelligent Well Completions as means to increase the recovery factor of the fields in Santos Basin. For this purpose, an R&D project for an Electric Inflow Control Valve for 4-1/2 in. tubing string size, following a methodology for Technology Readiness Level progression and reliability adopted by the biggest Brazilian oil company, was carried out from 2014 to 2019.
Environmental conditions, like pressures up to 16,500 psi, temperatures up to 150 °C [302 °F] and differential pressure opening of 1,500 psi, were challenging to the tool design. Additionally, during the electric valve’s development, there was no technical specification for Electric Intelligent Well Completions, so standards like API 17F for the vibration of the embedded electronics boards were also followed.
The tool was divided into physical modules as part of a development strategy. That revealed to be a good approach, as some of those demanding specifications were not yet met in 2019 for testing the fully assembled prototype in any Brazilian laboratory. Test fixtures for selected modules, which would later be integrated into the prototype, were developed so that those parts could be tested individually. The full-scale prototype was then fully assembled and mechanically tested to attend the specified operational static axial loads and cyclic loading and unloading. A second full-scale prototype was built to perform flow characterization and erosion tests. At the end of the development, a System Integration Test, with a spool of tube encapsulated cable simulating their predicted length in a field installation, was performed to prove the actuation and sensing functionalities of the two prototypes with the subsea control boards and human-interface machine.
Results from the testing program and the performance the electromechanical actuation led to a second phase of the Electric Inflow Control Valve development focusing on improving the flow portion to achieve the resistance to 3,000 psi of differential pressure while opening. Moving from a printed-circuit board to a hybrid technology for the valve’s embedded electronics is also a necessary step to increase the reliability of the system and meet the operator’s target. By using the same concept-proven electromechanical actuator, with the addition of a fail-safe device, an Electric Surface-Controlled Subsurface Safety Valve is being developed. Both projects are expected to achieve the TRL 6 by the end of 2024.
Abstract
Although Intelligent Completion is the fastest-growing completion solution worldwide, low reliability, multiplex limitation and data lack of existing solutions still hamper its full use. The inflow control valve is the main component to ensure selectivity between production zones for better reservoir management, contributing to an increase in the oil recovery factor of fields. In the same way, the downhole safety valve (subsurface safety valve) is the component responsible for preventing the uncontrolled flow of hydrocarbons to the external environment, through the production or injection tubing, and to allow safe closure in the event of catastrophic damage to subsea or surface equipment. However, low reliability, when being used in long-term operations, of hydraulic systems became inflow control valves and subsurface safety valves failures the most common cause of well intervention. Therefore, the objective of this paper is to present the R&D background, challenges, and lessons learned in the development of an electrically powered actuator with low power consumption applied to a prototype of an electric inflow control valve and a prototype of subsurface safety valve following technical specifications of ultradeep water Brazilian Pre-Salt wells. The paper also presents the methodology used to design the valves focused on high reliability in long-term operations (27 years of MTTF). In conclusion, the paper presents that this new downhole actuator concept is possible to implement in both valves for ultradeep water wells, being able to actuate with low power consumption.